AI and the Future of Manufacturing: 5 Key Insights from Industry Leaders
When one of the world’s largest manufacturing hubs, along with technology experts, gathers to discuss AI’s role in industrial transformation, you can expect more than buzzwords. In a recent panel, senior leaders who have launched AI initiatives at major manufacturers shared candid perspectives on both the obstacles and the opportunities surrounding next-generation technology. Below are the core insights they offered, along with a Customertimes success story that demonstrates AI in action.
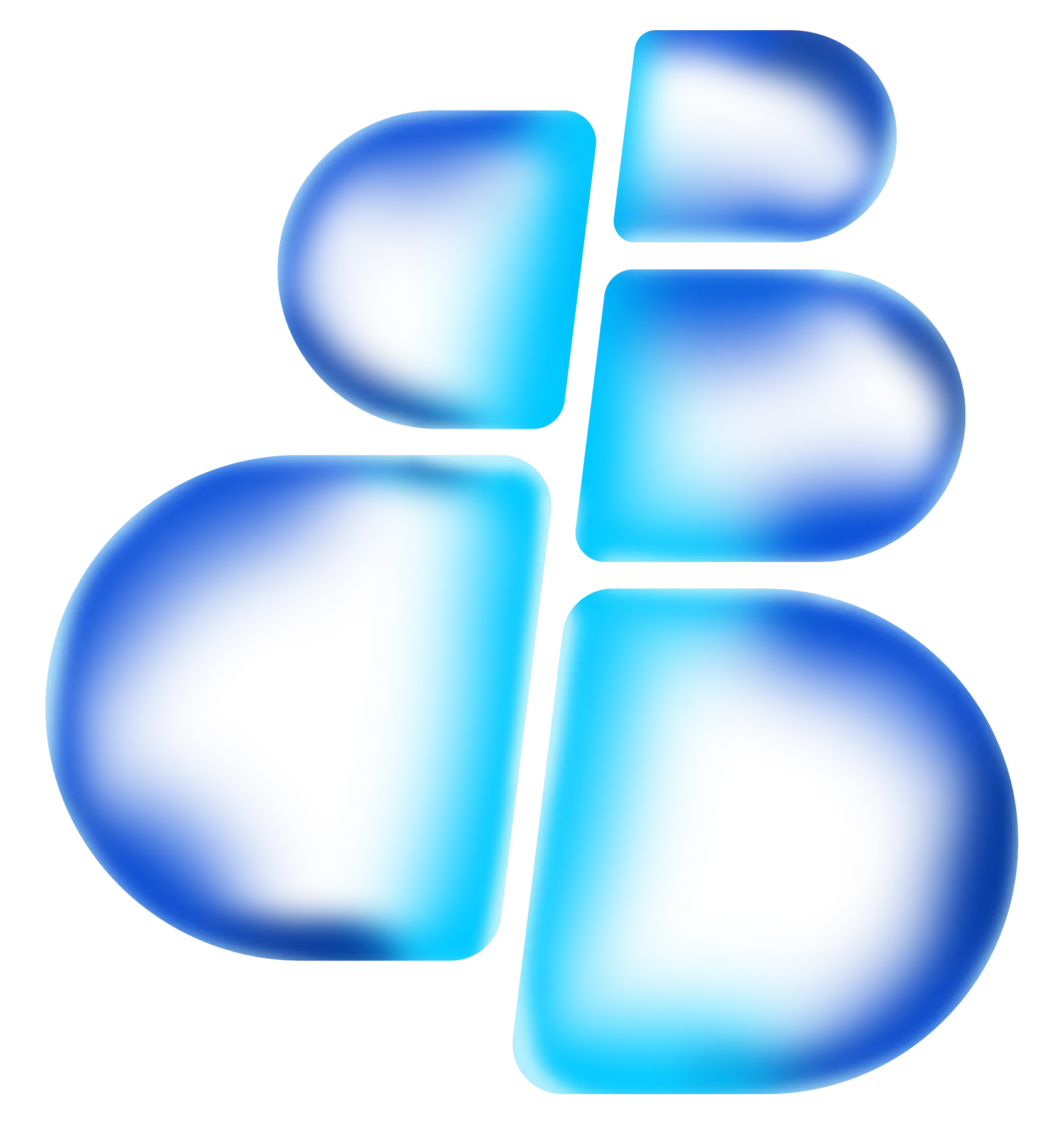
Beyond the Hype: AI as a Problem-Solving Tool
“We need to remember the traditional AI methods because they can still create a lot of value in manufacturing.”
—Cathy, CEO at a tech coalition.
Panelists emphasized that AI is far more than chatbots or flashy demos.In manufacturing, the most critical gains often come from “classic” AIdisciplines: machine learning for predictive maintenance, computer vision fordefect detection, and intelligent robotics for automated handling. While generative AI and large language models grab headlines, the real day-to-dayvalue in factories frequently lies in:
- Predictive Maintenance: Using historical data and sensors to predict failures before they happen.
- Computer Vision: Automating quality checks to prevent costly recalls.
- Demand Forecasting: Factoring in real-time variables (e.g., supply chain fluctuations, market trends) for accurate production planning.
Takeaway: Begin with practical, well-defined areas where AI can drive immediate efficiency or cost reduction, rather than defaulting o the latestheadline-grabbing application.
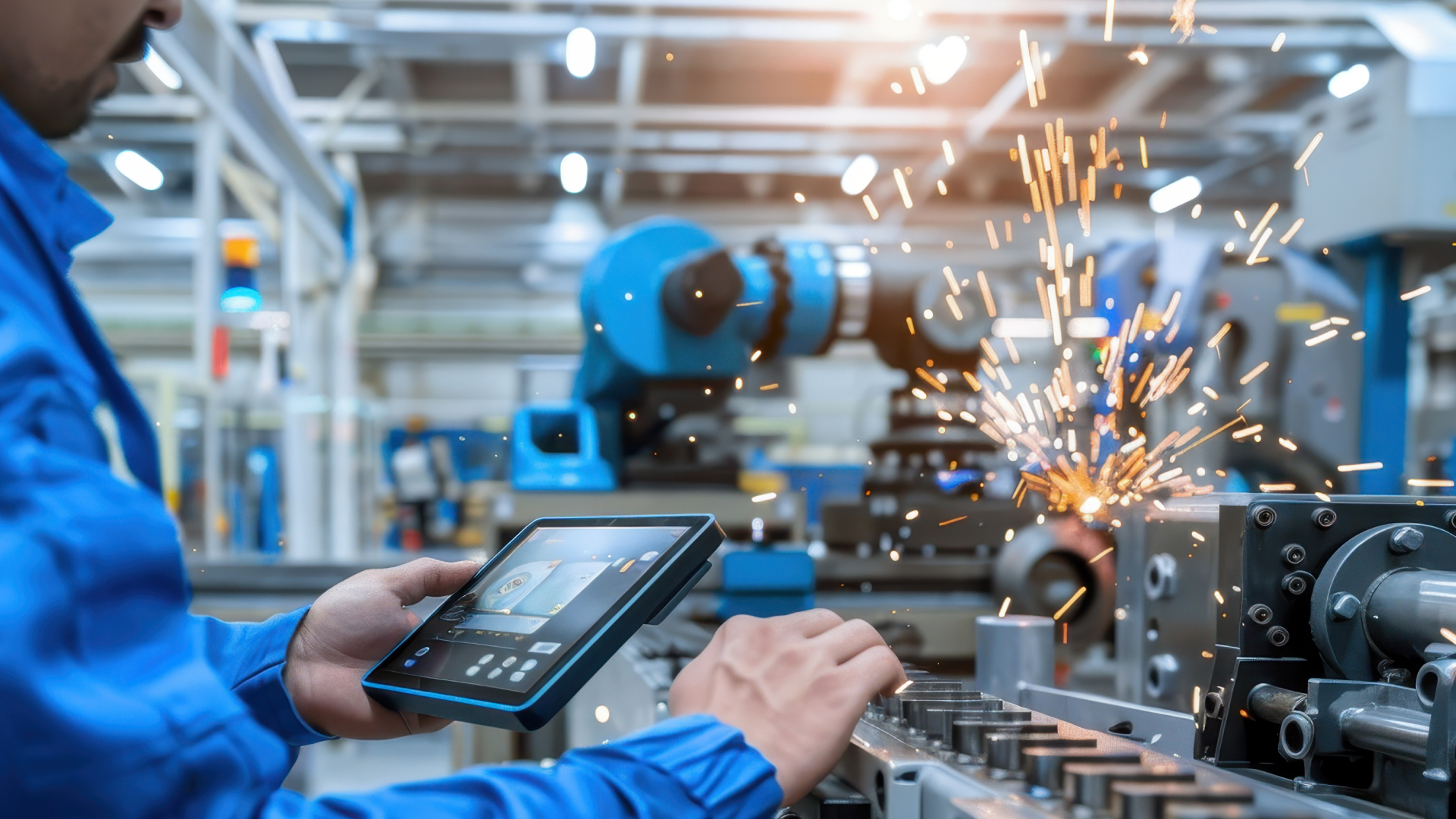
The Biggest Barrier Is Not the Technology - It’s Buy-In
“The hardest part about introducing AI in manufacturing is getting buy-infrom the business.”
—David, VP of IT and Digital Enablement.
One recurring theme was that cultural and organizational readiness often matter more than technical feasibility. Even the most robust AI models talls when field technicians or plant managers resist data-driven approaches or fear job displacement.
- Business Stakeholder Alignment: Leaders recommended “innovation-tailored business cases” that succinctly show value to CFOs and operations teams.
- Change Management: AI must be introduced with thoughtful engagement, addressing worries around job security and explaining how AI augments human roles rather than replaces them.
Takeaway: Secure buy-in early, define the specific business problem, and showhow AI solutions will enhance, not undermine, existing expertise.
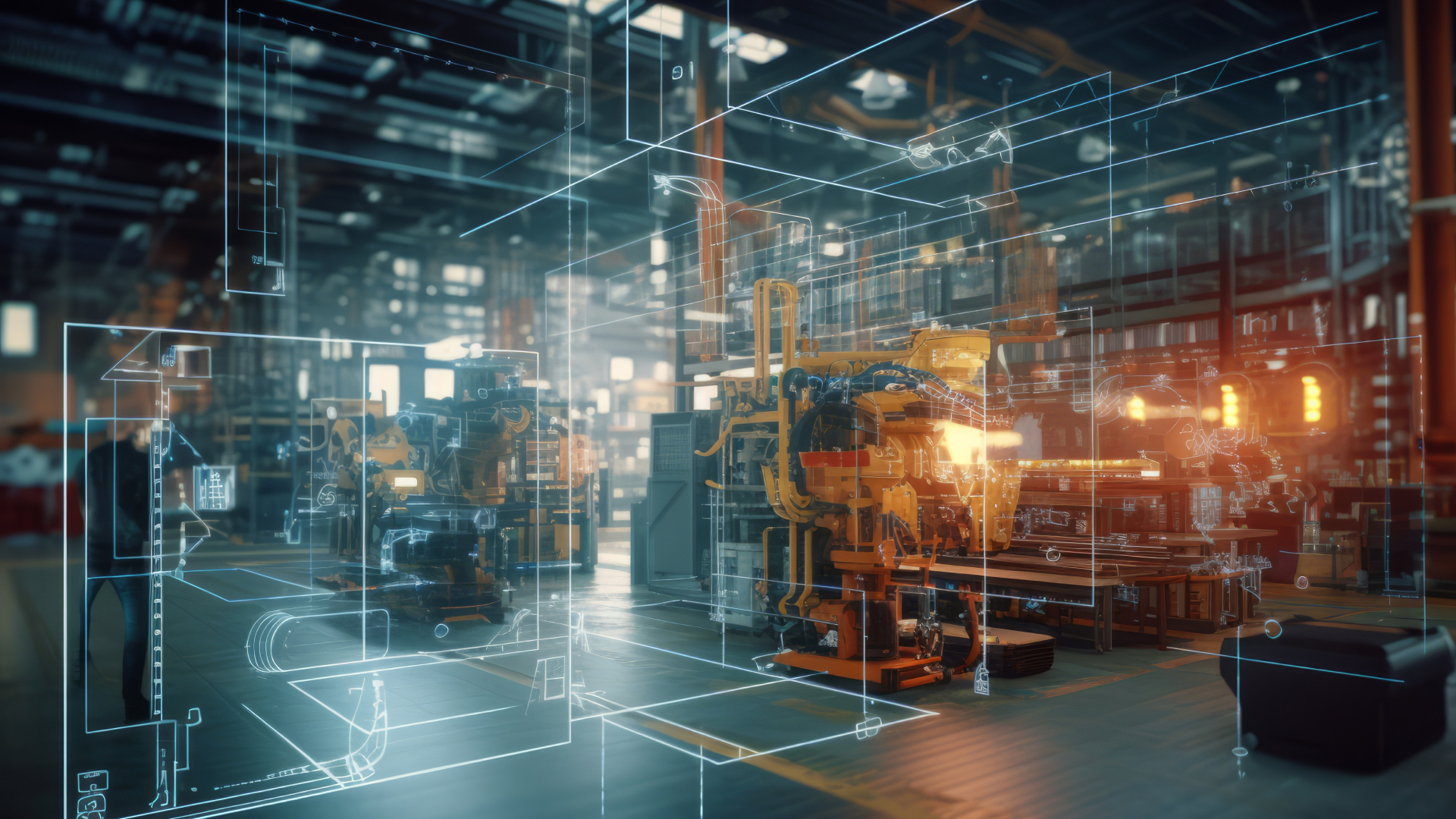
Starting Smart: Frameworks and QuickWins
Several speakers advocated a balanced approach that blends “quickwins” and “big bets.” Quick wins build momentum, while bigger, more transformative initiatives keep the organization from settling for only incremental gains.
“Don’t focus on ROI alone, you’re missing the real opportunity if all you want is an incremental improvement.”
—Sven, President of a manufacturing company.
- Prioritize Use Cases by Value and Data Availability: Aim for areas where you already have sufficient, somewhat clean data.
- Pilot with Purpose: Rather than scattering small experiments, pick a pilot project that can deliver visible results—like reducing production downtime or accelerating quoting cycles.
- Plan for Scalability: Proofs of concept (POCs) should come with a roadmap to full production, ensuring pilots integrate seamlessly into daily operations if successful.
Takeaway: Use a light but structured framework (research feasibility →proof of concept → pilot → scale) to ensure each initiative addresses a clearbusiness need before it expands.
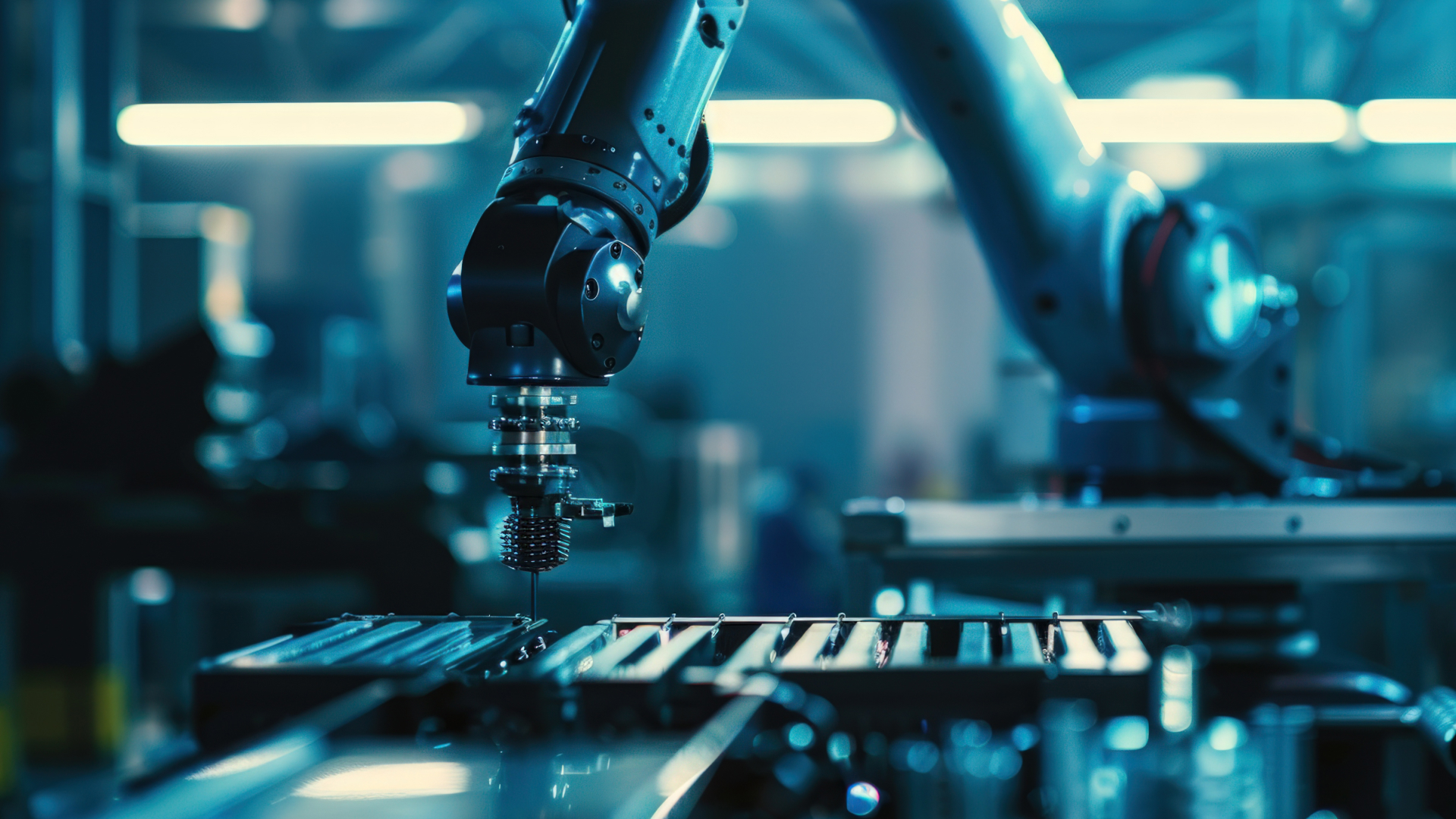
Spotlight Use Case: Customertimes& AI-Powered Predictive Maintenance
While the panel touched on multiple AI applications, predictive maintenance emerged as a high-impact example. Customertimes has worked with manufacturers across automotive, chemical processing, and food&beverage to deploy a real-time, data-driven solution that targets one of the biggest operational pains: unplanned downtime.
Check our Manufacturing use cases here
Business Challenge
Many manufacturers remain stuck in outdated, reactive approaches to equipment maintenance, often leading to:
- Unplanned Downtime: Lost production time and costly disruptions.
- High Repair Costs: Emergency fixes due to equipment breakdowns.
- Inefficient Maintenance: Rigid, time-based schedules that either under- or over-service machines.
Customertimes’ Predictive Maintenance Approach
- Sensor Integration: Real-time data capture (e.g., vibration, temperature) informs AI models.
- Machine Learning Analytics: Algorithms assess historical + real-time data to forecast potential failures.
- Dynamic Scheduling: Maintenance only occurs when needed—avoiding premature service or emergency repairs.
- Seamless ERP/CMMS Tie-In: Work orders and alerts sync with existing enterprise systems.
Results & Benefits
- 30–50% Reduction in Unplanned Downtime
- Up to 30% Maintenance Cost Savings
- Extended Equipment Lifespan by up to 25%
- Improved Safety (20–25% fewer incidents)
- ROI within 12–18 months of implementation
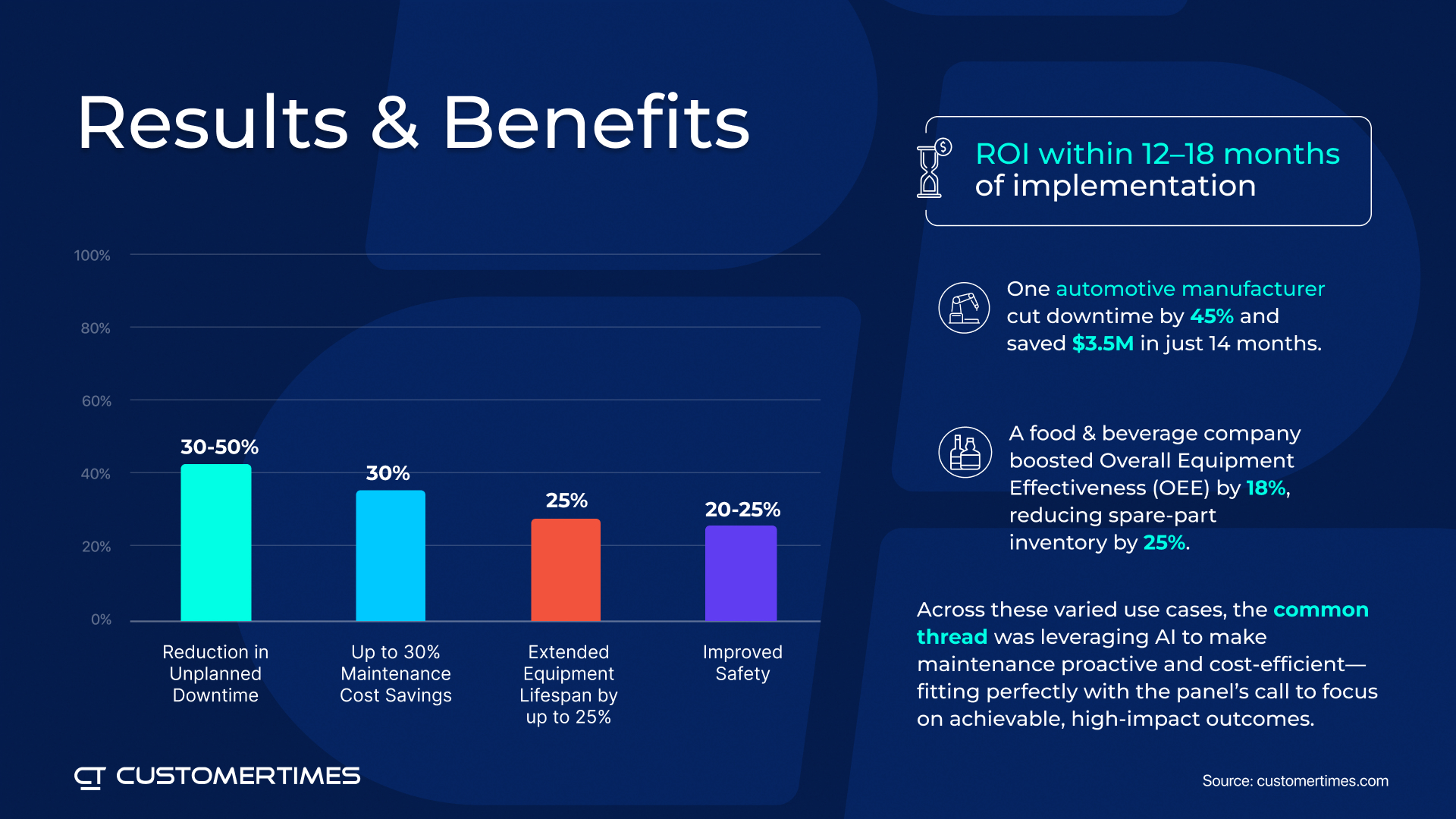
Conclusion: People Still Drive AI Success
Despite technological leaps, human expertise, oversight, and vision remain the heart of AI-driven manufacturing. As one panelist summed it up:
“If AI adoption were like dating, don’t spend forever on committees or short-sighted ROI hunts. Look for a real partnership that can transform your entire business—and commit to that journey.”
By balancing quick-win pilots with longer-term transformation—and by building the right cultural consensus—manufacturers can use AI to cutcosts, reduce downtime, and gain a critical competitive advantage. With success stories like Customertimes’ predictive maintenance solution, it’s clearthat strategic AI adoption is no longer optional—it’s key tofuture-proofing manufacturing operations.
Next Steps for Manufacturing Innovators
- Assess Data Readiness: Identify where you have enough reliable data to support AI-driven solutions—predictive maintenance is often a great starting point.
- Engage a Cross-Functional Team: Gather input from operations, IT, and finance to ensure alignment on business outcomes.
- Define Clear Metrics: Whether it’s reduction in downtime or faster quoting, set tangible KPIs to measure success.
- Plan for Scale: Consider how a successful pilot will integrate into broader workflows across multiple facilities.
If you’re looking to explore how AI can bolster equipment reliability or streamline other critical processes, the path is open. From predictive maintenance to advanced robotics, the potential gains are too large to ignore—and the time to start is now.